The Science Behind Porosity: A Comprehensive Overview for Welders and Fabricators
Understanding the detailed devices behind porosity in welding is important for welders and producers pursuing remarkable craftsmanship. As metalworkers delve right into the depths of this phenomenon, they discover a world regulated by numerous factors that affect the development of these small voids within welds. From the make-up of the base materials to the details of the welding process itself, a wide variety of variables conspire to either aggravate or minimize the presence of porosity. In this detailed overview, we will certainly unravel the science behind porosity, exploring its impacts on weld quality and introduction advanced strategies for its control. Join us on this trip with the microcosm of welding flaws, where accuracy meets understanding in the quest of remarkable welds.
Recognizing Porosity in Welding
FIRST SENTENCE:
Assessment of porosity in welding reveals essential understandings right into the integrity and quality of the weld joint. Porosity, defined by the visibility of cavities or voids within the weld metal, is an usual concern in welding processes. These spaces, otherwise effectively addressed, can jeopardize the structural stability and mechanical residential or commercial properties of the weld, resulting in potential failures in the finished item.
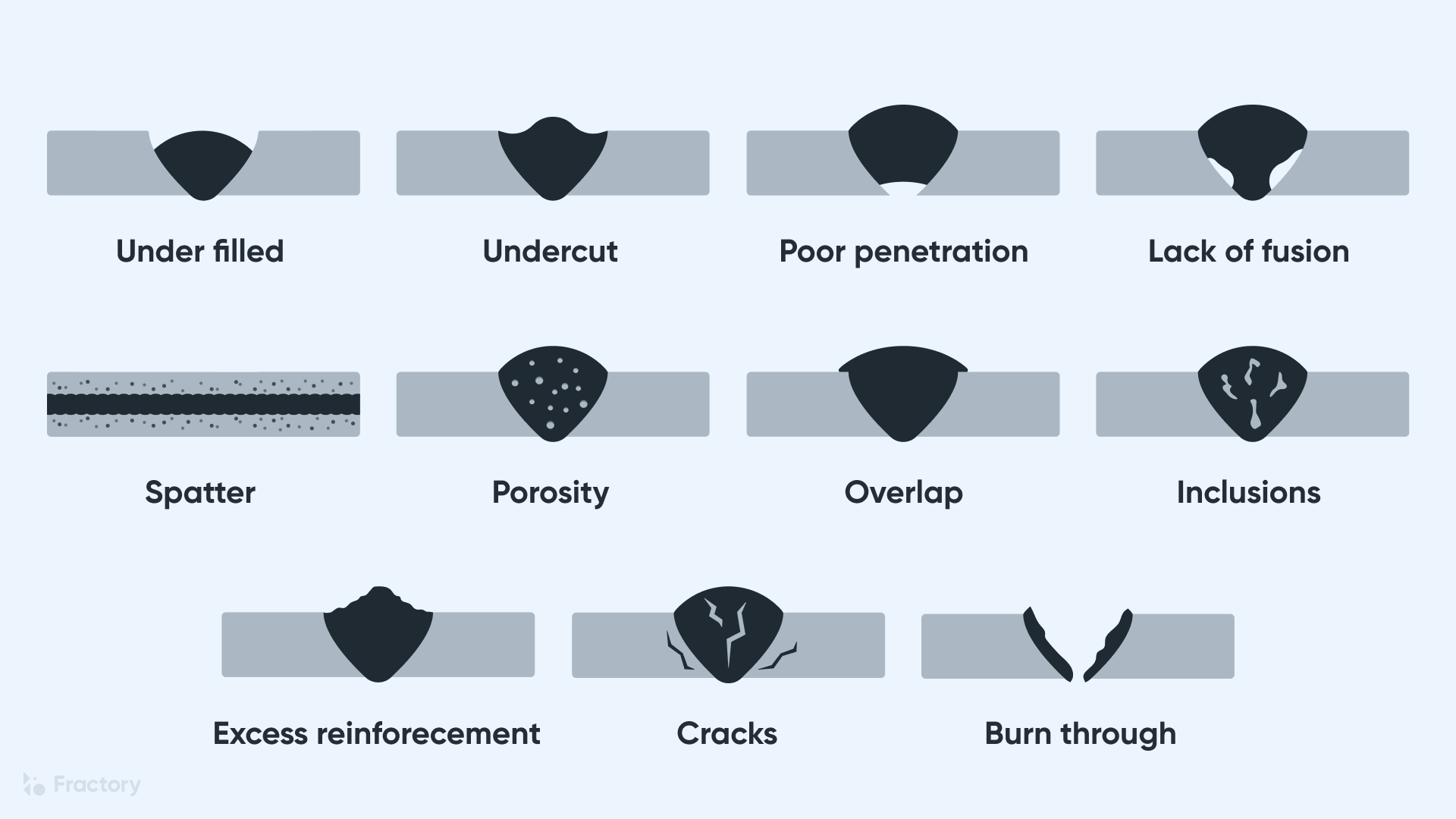
To find and quantify porosity, non-destructive testing approaches such as ultrasonic screening or X-ray assessment are frequently used. These methods permit for the recognition of internal issues without endangering the integrity of the weld. By analyzing the size, form, and distribution of porosity within a weld, welders can make educated choices to improve their welding processes and accomplish sounder weld joints.
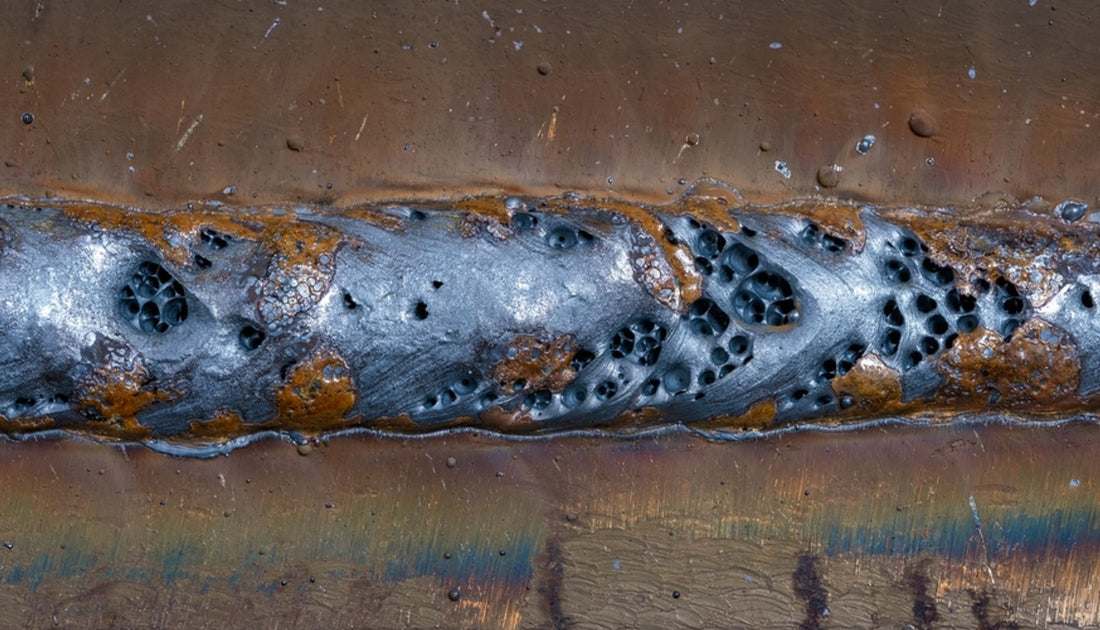
Variables Affecting Porosity Development
The event of porosity in welding is influenced by a myriad of aspects, varying from gas shielding effectiveness to the details of welding specification settings. One critical variable contributing to porosity formation is poor gas shielding. When the shielding gas, typically argon or carbon dioxide, is not successfully covering the weld pool, climatic gases like oxygen and nitrogen can pollute the liquified steel, bring about porosity. Furthermore, the tidiness of the base materials plays a considerable role. Contaminants such as corrosion, oil, or wetness can vaporize throughout welding, producing gas pockets within the weld. Welding specifications, consisting of voltage, current, take a trip speed, and electrode type, likewise effect porosity development. Using improper settings can create excessive spatter or warmth input, which in turn can lead to porosity. The welding strategy used, such as gas steel arc welding (GMAW) or go right here secured metal arc welding (SMAW), can influence porosity development due to variations in warm distribution and gas protection. Comprehending and controlling these elements are vital for reducing porosity in welding procedures.
Impacts of Porosity on Weld Quality
Porosity formation dramatically endangers the structural honesty and mechanical residential or commercial properties of bonded joints. When porosity is present in a weld, it creates voids or dental caries within the material, decreasing the total stamina of the joint. These spaces serve as stress focus factors, making the weld Read More Here extra vulnerable to breaking and failing under tons. The presence of porosity additionally damages the weld's resistance to deterioration, as the caught air or gases within deep spaces can respond with the surrounding environment, leading to deterioration over time. Additionally, porosity can prevent the weld's capacity to endure pressure or influence, further threatening the general quality and integrity of the welded structure. In important applications such as aerospace, vehicle, or architectural buildings, where safety and security and durability are extremely important, the harmful effects of porosity on weld top quality can have serious consequences, emphasizing the relevance of reducing porosity with correct welding methods and treatments.
Methods to Decrease Porosity
To boost the high quality of bonded joints and make sure structural integrity, welders and producers employ particular methods aimed at lowering the formation of spaces and cavities within the product during the welding process. One reliable approach to minimize porosity is to ensure proper material prep work. This consists of complete cleaning of the base metal to get rid of any kind of pollutants such as oil, grease, or wetness that could contribute to porosity formation. Furthermore, making use of the proper welding specifications, such as the correct voltage, existing, and travel rate, is essential in protecting against porosity. Preserving a constant arc size and angle throughout welding additionally aids lower the probability of porosity.

Additionally, picking the appropriate securing gas and preserving correct gas flow rates are important in minimizing porosity. Making use of the proper welding technique, such as back-stepping or employing a weaving movement, find out here now can additionally help distribute warmth evenly and lower the opportunities of porosity development. Ensuring proper ventilation in the welding atmosphere to remove any prospective resources of contamination is important for achieving porosity-free welds. By applying these methods, welders can successfully reduce porosity and generate high-grade welded joints.
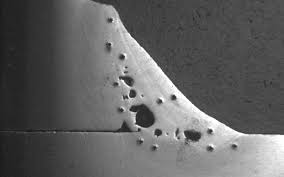
Advanced Solutions for Porosity Control
Applying cutting-edge technologies and ingenious methods plays an essential role in attaining remarkable control over porosity in welding processes. Furthermore, using sophisticated welding techniques such as pulsed MIG welding or modified atmosphere welding can likewise aid minimize porosity concerns.
An additional sophisticated option entails the use of sophisticated welding equipment. Using devices with integrated features like waveform control and innovative power sources can enhance weld quality and reduce porosity dangers. The application of automated welding systems with specific control over specifications can significantly decrease porosity problems.
In addition, including advanced surveillance and examination modern technologies such as real-time X-ray imaging or automated ultrasonic testing can help in identifying porosity early in the welding procedure, permitting prompt rehabilitative activities. On the whole, integrating these sophisticated services can significantly improve porosity control and boost the total quality of bonded components.
Final Thought
Finally, understanding the science behind porosity in welding is vital for welders and producers to produce top notch welds. By recognizing the elements influencing porosity development and executing methods to minimize it, welders can improve the total weld quality. Advanced options for porosity control can further boost the welding process and make sure a solid and reliable weld. It is essential for welders to constantly enlighten themselves on porosity and execute ideal methods to attain optimum results.